The micro CNC machining technology adopts a fully automatic method to super-finish the surface of metal parts. Through a kind of mechanochemical action, the material of 1-40μm on the surface of the metal parts is removed, and the surface quality of the processed surface reaches or is better than the N1 level of the ISO standard. Micro CNC machining technology is mainly used in the two fields of ultra-precision polishing and ultra-precision brightening. Ultra-precision polishing automates the traditional manual polishing process; The super-precision brightening generates a new surface topology.
An outstanding advantage of micro-CNC machining technology is that it can give new microstructures to the surface of the part. These microstructures can improve the adaptability of the part surface to specific application functions. Such as reducing friction and mechanical differences, improving wear resistance, and improving the deposition performance of the surface before and after coating.
In general, super-precision brightening can remove secondary micro-rough surfaces. The thickness of the secondary rough surface is between 0 and 20 μm, located between the peaks of the primary micro rough surface of the part surface. The super-finishing polishing removes the primary microscopic rough surface partially or entirely, and its value is between 10 and 40 μm. Of course this depends on the initial state of the part material surface.
The materials that can be processed by microfabrication technology so far are: Annealed and hardened steel, Copper and copper alloys, cast iron, Inconel nickel alloy (nickel-based alloy), titanium, Pretreatment (PVD, CVD, electroplating) before and after surface hard coating treatment.
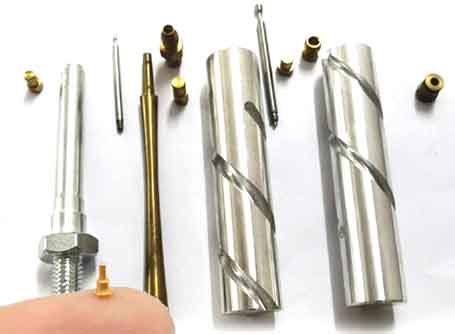
Micro CNC machining parts technology