The use of short cutting tools is the main feature of five-axis machining. Short tools will significantly reduce tool deviation, thereby obtaining a good surface quality, avoiding rework, reducing the amount of welding rod used, and shortening the processing time of EDM. When considering five-axis machining, the goals of using five-axis machining molds must be considered:
Use the shortest cutting tool possible to complete the processing of the entire workpiece. It also includes reducing programming, clamping and processing time but can get a more perfect surface quality.
As long as the workpiece cavity is not very deep (relative to the tool diameter), a three-axis tool path (2, 3, 5) is sufficient. If the workpiece cavity is very deep and has very narrow parts, it is not enough to use a pure three-axis tool path to complete the entire finishing. In this case, poor surface quality and long processing time ensue. Figure 1 is the case of a three-axis tool path. Here, the shortest tool must be very long in order to be able to machine all areas of the workpiece in the vertical direction.
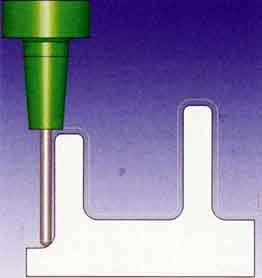
3-axis machining path of short tool
Figure 1, Three-axis machining path
When using a shorter tool, the spindle should be tilted to ensure that the special area of the workpiece can be processed. 3+2 axis machining is usually considered as setting a constant angle to the spindle. Complex workpieces may require many oblique views to cover the entire workpiece, but this will cause tool paths to overlap and increase machining time.
In addition, all the oblique views are difficult to accurately combine, so the workload of manual polishing will increase, and at the same time, it will greatly increase the movement in and out, which often leads to surface quality problems and more tool movement.
Figure 2, 3+2 axis tool pathFinally, programming in this way will interfere with each other and is time-consuming, and the sum of all views often cannot cover the entire geometry. Figure 2 demonstrates four workpiece views, but there is still an area in the center of the workpiece that cannot be covered. This area still needs an additional oblique view.
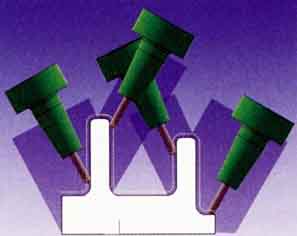
3+2 axis short tool machining path
Figure 3, 5-axis tool path
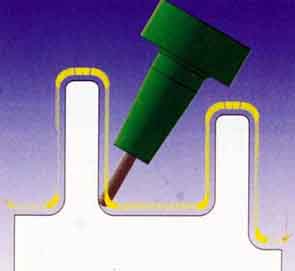
5-axis short tool machining path
In order to overcome the shortcomings of 3+2 axis machining, five-axis simultaneous machining may be a better choice, not to mention that some five-axis machine tools also have some functions specially designed for the mold industry. Five-axis linkage machining can coordinate three linear axes and two rotary axes to make them move at the same time, which solves all the problems of 3-axis and 3+2 axis machining. The tool can be very short, there is no overlapping of views, the possibility of missing the processing area is less, and the processing can be performed continuously without additional import and export (see Figure 3).