Turbine impellers with complex shapes need to be machined with a 5-axis milling machine to be able to machine every corner of its geometry.
In a modern design system, the geometry that needs to be processed is designed by the CAD system, and then converted into the tool trajectory in the CAM system. The output result is converted into the movement of each of the 5 axes of the milling machine through a post-processing program. For turbomachinery impellers, it is necessary to consider dedicated CAM software. In terms of technology, impeller processing is mainly composed of the following 5 distinct operations:
1, the flow path between the rough machining blades
2, milling the hub part
3. Milling round inlet and outlet edges
4. Finishing the surface of the impeller blade with a small amount of cutting
5. Variable radius fillet processing of the root of the impeller blade
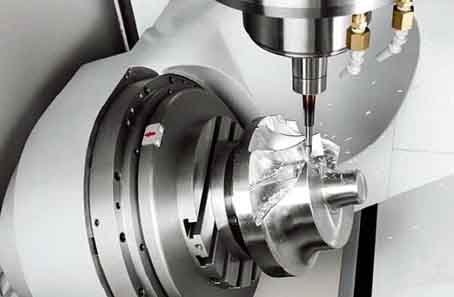
5 axis milling of turbine impeller
Special attention should be paid to areas on the surface of the impeller blades that cannot be reached by the tool. Because at this time it is easy to cause interference between the cutter and the adjacent blades.
Before adopting 5-axis CNC machining centers, most turbomachinery manufacturers used 3-axis or 4-axis machine tools to process impellers, and most of them used point machining. That is, every point on the blade surface is processed into a point by the tool tip. When the tool moves along the surface of the blade, it will leave some pits or residual sharp corners, and the height of these pits or sharp corners depends on the programming skills. Point processing is also a feasible method, but this method has some unavoidable disadvantages:
1. The surface of the impeller blade is not smooth, leaving some small grooves. These small grooves must be parallel to the flow direction (see Figure 1).
2. For blades with severe curvatures, due to the close spatial distance of the impeller blades, it is difficult to avoid interference with adjacent blades during processing.
3. If you want to reduce the influence of the groove on the flow field, a long processing time is required. In other words, the tool must move many times around the impeller blades.