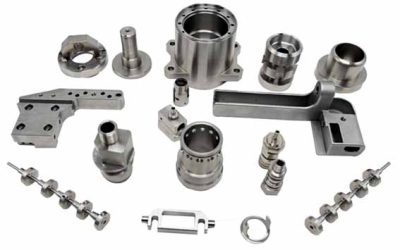
Stainless steel parts
How to machine stainless steel parts? CNC Machining Technology and Application of Stainless Steel Parts
Stainless steel is a versatile machining material that can be widely used where strength and resistance to heat and corrosion are essential. However, the same properties that make stainless steel alloys exceptional structural materials also complicate the processes used to machine them. A careful combination of cutting tool properties, geometries and the application of cutting parameters can significantly increase the productivity of stainless steel machining operations.
AUSTENITIC STAINLESS STEELS
They make up the 200 and 300 series. Their general characteristics are:
Excellent corrosion resistance.
Highly formable.
Not magnetic.
Cold work hardened (Cannot be heat treated).
Excellent weldability.
They have the ability to be functional in extreme temperatures.
They are prone to corrosion cracking.
Composition:
They are obtained by adding elements such as nickel, manganese and nitrogen. The chromium content generally varies between 16 and 26%. The carbon content is in the range of 0.03 to 0.08%. Chromium provides part of the oxidation resistance and also molybdenum in some of its alloys.
They are used in:
Shafts, valves, screws, bushings, nuts, chemical equipment, equipment for hospitals, marine applications, aviation components, food and beverage processing equipment, architectural ornaments, cryogenic vessels, temporary prosthetics, etc.
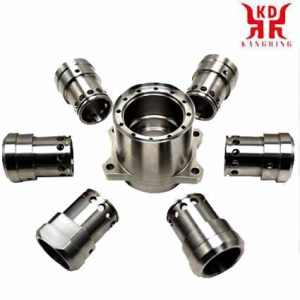
304 stainless steel parts
Alloy evolution
Basic stainless steel alloys are classified as ferritic or martensitic. Ferritic alloys with a chromium content of 10-12 percent cannot be quenched. Martensitic alloys have a higher chromium and carbon content than ferritic stainless steels, as well as manganese and silicon content, resulting in an alloy that can be tempered by heat treatment. Today, ferritic and martensitic stainless steel alloys are not widely used generally in industrial settings, but rather in household items such as kitchen or garden tools.
As the use of stainless steel has evolved, alloys are frequently applied in situations that require mechanical strength as well as resistance to corrosion. To improve the strength of alloys, metallurgists have added nickel to alloys, so that iron / chromium alloys have been converted to iron / chromium / nickel alloys. These materials are called austenitic stainless steels and are now common in industrial applications where strength and resistance to corrosion and heat are required. These alloys are normally used in the petrochemical industry, in the food sector, since hygiene standards require resistance to corrosion and in general machinery designed for use in harsh environments.
Inevitably, increasing the performance capabilities of an alloy, such as stainless steel, also multiplies machining problems. The corrosion resistance characteristics of martensitic and ferritic stainless steel alloys are basically chemical properties, and as a result these alloys are not much more difficult to machine than plain steels. However, the additions of nickel and other elements to austenitic stainless steels produce higher hardness, toughness, resistance to deformation, and thermal properties that decrease machinability.
zero stainless steel 304 vs stainless steel 316
They are the most common stainless steel options. On a mechanical level they are quite similar to each other.
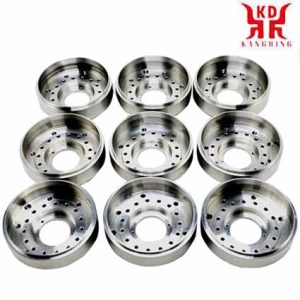
316 stainless steel parts
316 is obtained by adding Molybdenum, which improves mechanical resistance at high temperatures compared to 304 (although its melting point is slightly lower) and resistance to corrosion against various aggressive chemicals, acids and saline atmosphere. However, 304 is a little cheaper (important in the manufacture of large series).
Low carbon “L” types (304L and 316L) have higher corrosion resistance than basic types and reduce the possibility of corrosion cracking. They are also more suitable for welding but less mechanically resistant. The “H” types that indicate a higher amount of carbon are more suitable for high temperatures.
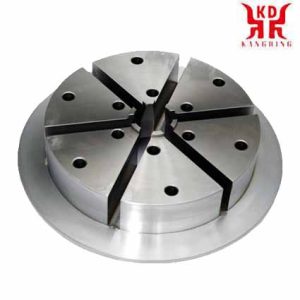
416 stainless steel parts
MARTENSITIC STAINLESS STEELS
They represent a portion of the 400 series (the other portion corresponds to ferritics).
Its main characteristics are:
They can be hardened by heat treatment therefore high levels of mechanical resistance and surface hardness can be developed.
They have greater mechanical, wear and fatigue resistance than austenitics.
Moderate corrosion resistance (less than austenitics).
Good ability to be machined.
They are magnetic.
Due to the high carbon content and the nature of its hardness, it is poorly weldable.
Composition:
They are essentially alloys of chromium and carbon. The chromium content is generally 10.5 to 18% and the carbon content is high, reaching values of up to 1.2%.
They are used in:
Machinery parts, pump shafts, screws, bushings, cutlery, hardware, jet engine parts, mining machinery, rifles, valves, aircraft accessories, inserts for fire extinguishers, parts for gas or steam turbines, rivets, etc
416 stainless steel
It is a version of type 410 (most common martensitic stainless steel), where sulfur and phosphorus are added to achieve better machining characteristics (the 400 series is already easier to machine than the 300 series). It has less ductility and formability than 410. It is more economical than the 300 series. They are for use in moderately corrosive environments. It can develop an excellent combination of mechanical resistance and hardness through adequate heat treatment.
440C stainless steel
It is possible to increase the hardness with respect to 410 by adding Carbon and the corrosion resistance is increased thanks to the chromium. Therefore they have high hardness, resistance to abrasion and wear, and good resistance to corrosion. Low machinability. This stainless steel achieves the highest hardness once hardened and the greatest resistance to wear of any steel resistant to corrosion or heat. It is widely used to make knives, bearings, measuring instruments, valve seats, etc.
PRECIPITATION HARDENED STAINLESS STEELS
This family offers an alternative to austenitic stainless steels when it is desired to combine high mechanical characteristics, good corrosion resistance and good machinability. Precipitation-hardenable steels are patented and are often designated by the initials of the manufacturing company.
Its main characteristics are:
Good corrosion resistance.
Good weldability.
They are magnetic.
Very high mechanical strength obtained from hardening by heat aging treatment.
They maintain a high mechanical resistance even at high temperatures.
Composition:
They are mainly iron-chromium-nickel alloys. The chromium content is generally 12 to 18% and the nickel content is between 4% and 9%.
They are used in:
Mainly in the aerospace and military industry (missiles) for structural components and in motor shafts, instruments, gears, etc.
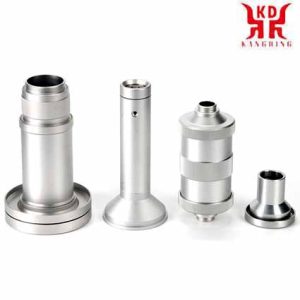
440C stainless steel parts
630 stainless steel (17-4PH)
It offers high mechanical strength and toughness with excellent corrosion resistance. It can be hardened by aging in a simple way and at a low temperature, which avoids deformations. It is easy to machine before being heat treated.
It has a better behavior in all corrosive environments than 400 series stainless steels, and similar to 304 stainless steel. It can be welded. It may lose the high mechanical strength if heated above the precipitation hardening temperature (495-620 ° C).
Know the alloys
Until recently, machining of austenitic stainless steel was not well understood. The tool manufacturers assumed that since the alloys were stronger, the mechanical cutting forces would be higher and therefore stronger negative geometry tools would have to be applied that would lower the cutting parameters. However, this method produced tools with short life, long chips, frequent burrs, unsatisfactory surface roughness, and unwanted vibrations.
In reality, the resulting mechanical cutting forces in austenitic stainless steel are not much greater than those normally used when machining traditional steels. Most of the additional energy consumption required to machine austenitic stainless steels is the result of their thermal properties. Machining is a deformation process, and when machining a strain-resistant austenitic stainless steel, the operation generates excessive heat.
Evacuating that heat from the cutting area is vital. Unfortunately, in addition to being resistant to warping, austenitic stainless steel also has low thermal conductivity. Chips created during the machining of plain steels absorb and transport heat, but austenitic stainless steel chips absorb heat only to a limited extent. Also, since the part itself has poor thermal conductivity, excess heat enters the cutting tool, resulting in a short tool life.
Tool manufacturers created carbide substrates to provide enough toughness to withstand the high temperatures that are generated during machining of stainless steel. At the same time, the composition of the substrate is just as important as the edge preparation. A sharper-edged tool cuts stainless steel more than warps it, thereby reducing heat generation.
Aggressive cutting parameters
In the interest of heat removal from the cutting zone, the most efficient way to machine stainless steel is to employ the greatest depths of cut and feeds. The goal is to maximize the amount of heat that is removed from the chips. Since the poor thermal conductivity of stainless steel limits the amount of heat that can be absorbed by each cubic millimeter of chip material, creating longer chips, with more cubic millimeters in volume, will remove more heat. Using greater depths of cut will also reduce the number of passes required to complete a part, an important aspect since austenitic stainless steel has a tendency to warp or harden when machined.
There are practical limitations to these aggressive machining methods. Surface finish requirements, for example, will limit maximum feed. The available power of the machine, as well as the force of the cutting tool and the piece, also impose limitations on the aggressiveness of the parameters that can be used.
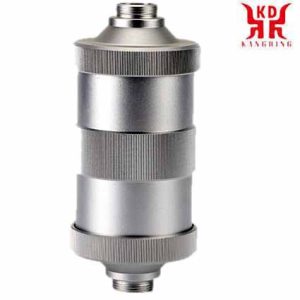
Surface finishing of stainless steel parts
Refrigerant strategies
The problematic thermal properties of austenitic stainless steel alloys suggest that the application of coolant is almost always critical to successful machining. The coolant must be of high quality, with a minimum oil content of eight to nine percent in a water / oil emulsion, compared to the three to four percent oil content typical of many machining operations.
How the coolant is applied is also important. The higher the pressure when applying the coolant to the cutting zone, the better it will do its job. Technologies like Seco’s Jetstream Tooling®, which apply a high pressure coolant flow directly to the cutting zone, are even more effective.
Coatings vs. tool wear
A hard coating deposited on the surface of the tool substrate reinforces the hot hardness on the tool surface and improves service life in high temperature environments. However, a coating, in general, must be thick to insulate the tool substrate from heat, and a thick coating does not adhere well to very sharp geometry. Cutting tool manufacturers are responsible for designing coatings that are thin but provide a good barrier against heat.
Austenitic stainless steels have high ductility and a tendency to stick to the cutting tool. Applying a coating can also prevent bond wear, something that occurs when machined material sticks and builds up on the cutting edge. Adhered material can then break sections of the cutting edge, leading to poor surface finish and tool failure. The coating can provide lubricity that limits stick wear, while the higher cutting speeds also serve to reduce the stick wear mechanism.
Some austenitic stainless steel alloys contain hard and abrasive inclusions, so increasing the abrasive resistance of the cutting tool, in combination with a hard coating, can benefit the life of the tool.
Chipping occurs due to the alloys’ tendencies to warp and shear self-hardening during machining.
Chipping can be described as highly localized extreme friction wear, and can be mitigated by applying suitable coatings and other actions such as varying the depth of cut to widen the wear zones on the cutting edge.
Tool development
Tool builders focus current cutting tool development on finding a balance between tool properties that will provide optimum performance on a specific material to be machined. Carbide quality research seeks a balance between hardness and toughness, so that a tool is not so hard that it fractures but is tough enough to resist deformation.
Similarly, a sharp edge geometry is preferable, although it is not as strong as a rounded edge. Therefore, the goal of developing cutting edge geometries is to create tools with a balance between sharp edge and maximum possible robustness.
As part of the development process, tool manufacturers are reviewing their guidelines on tool applications.
Current recommendations on machining parameters are based, for the most part, on the toughness and hardness of traditional steels, without taking into account the thermal factors that are so important during machining of austenitic stainless steels and other high-grade alloys. performance. Recently, tool manufacturers have begun working with academic institutions to review tool testing procedures to account for the thermal characteristics of certain materials.
The new guidelines reflect the creation of new reference materials. Traditionally, machinability standards were established according to a reference material, an alloy steel, and according to the mechanical loads produced during machining. There is now a separate set of reference material for austenitic stainless steels, for which reference values have been established for speed, feed and depth of cut. With respect to the reference material, the balance or calibration factors are applied to determine the changes in the base values that will achieve optimal productivity in materials with different machining characteristics.
Specific geometries for specific materials
Many cutting tools provide very acceptable performance on various materials and under a wide variety of cutting conditions and machining parameters. For one-time jobs with moderate productivity and quality requirements, these tools can be a cost-effective option. To achieve maximum performance, however, tool manufacturers continue to try to manipulate and balance a wide variety of cutting elements to create tools that offer high productivity and process reliability for specific materials to be machined.
The basic elements of a tool include the substrate, coating, and geometry. Each of them is important, and in the best tools they work as a system that produces results beyond the sum of all the separate pieces.
There are differences between the functions that the parts of the tool have. The substrate and coating have passive functions and are designed to offer a balance between hardness and toughness, as well as to resist high temperatures, chemicals, adhesion and abrasive wear. Tool geometry, on the other hand, plays an active role because by altering the geometry you can change the amount of metal that can be removed in a given period of time, the amount of heat that is generated, how chips are formed, and what surface finish can be achieved.
Some basic examples of how performance changes according to different geometries include inserts with traditional Seco turning geometry called e.g. M3 and M5, which have negative cutting edge geometries (0˚ angular distance) and -T edges between the cutting edge and cutting area of the tool. The M3 geometry is a versatile semi-roughing geometry that offers good wear life and chip breakage on a wide range of machining materials. The M5 geometry is designed for demanding high feed roughing applications, combining high cutting edge strength with relatively low cutting forces.
Although versatile, M3 and M5 geometries are robust, not completely sharp-edged, and generate a fair amount of heat as they deform during machining of austenitic stainless steels. In comparison, the tool designs that can be most effective in machining stainless steel include Seco’s MF4 and MF5 geometries, which have the sharpest edge, with positive T-edges. The geometries have been designed to be open and easy to machine to facilitate medium roughing and finishing operations on steels and stainless steels. The MF5 geometry is especially effective in high feed applications.